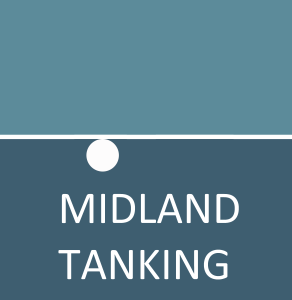
Waterproofing Systems
The waterproofing systems we install
Midland Tanking is the Midlands’ most recommended waterproofing specialist. The waterproofing systems we can install cover the whole waterproofing spectrum. We are approved system designers and installers of the full range of each of the below waterproofing system suppliers and their products:
We are CHAS Elite accredited and are also a full member of the Property Care Association (PCA) and the UK governments Trustmark Scheme
How we choose the right the system
Each system that we design is fully bespoke for the project on which we are working. Waterproofing system design and installation generally cannot be put into a box because of the many varying factors that effect the risk profile of an underground project.
Before any design can be carried out a waterproofing system risk assessment is carried out by one of our CSSW qualified designers, following our very simple design philosophy:
“All designs begin with the prevailing ground conditions. The ground conditions inform the risk profile, the risk profile informs the design & installation process”
Types of waterproofing system
Waterproofing design in the UK is laid out in BS 8012:2022 Protection of below ground structures against water ingress. Within this document there are three types of waterproofing system defined, those are referred to as Type A, Type B and Type C.
To comply to recent changes to third party warranty providers (NHBC, LABC, Premier Guarantee etc) a new underground structure must have two forms of waterproofing. Below are the definitions and types of waterproofing system we install.
If you want more information or advise on how to waterproof your underground project get in touch with our certified designers now.
Type A – Barrier protection
A type A system is one that seeks to prevent any water ingress from the ground by creating a physical barrier to the water. This can be internal or external and is applied at the time of the build. There are several methods of achieving this:
- Bitumen coating
- Bentonite clay coatings
- External cementitious slurry
- Internal cementitious slurry
- Combinations of the above
Type A waterproofing systems are only appropriate for new build basements as existing basements don’t usually have the strength within the structure to allow the barrier to bond and resist hydrostatic pressure.
External bentonite waterproofing
A high performance self swelling, self healing waterproofing membrane is applied to the external face of the basement walls.
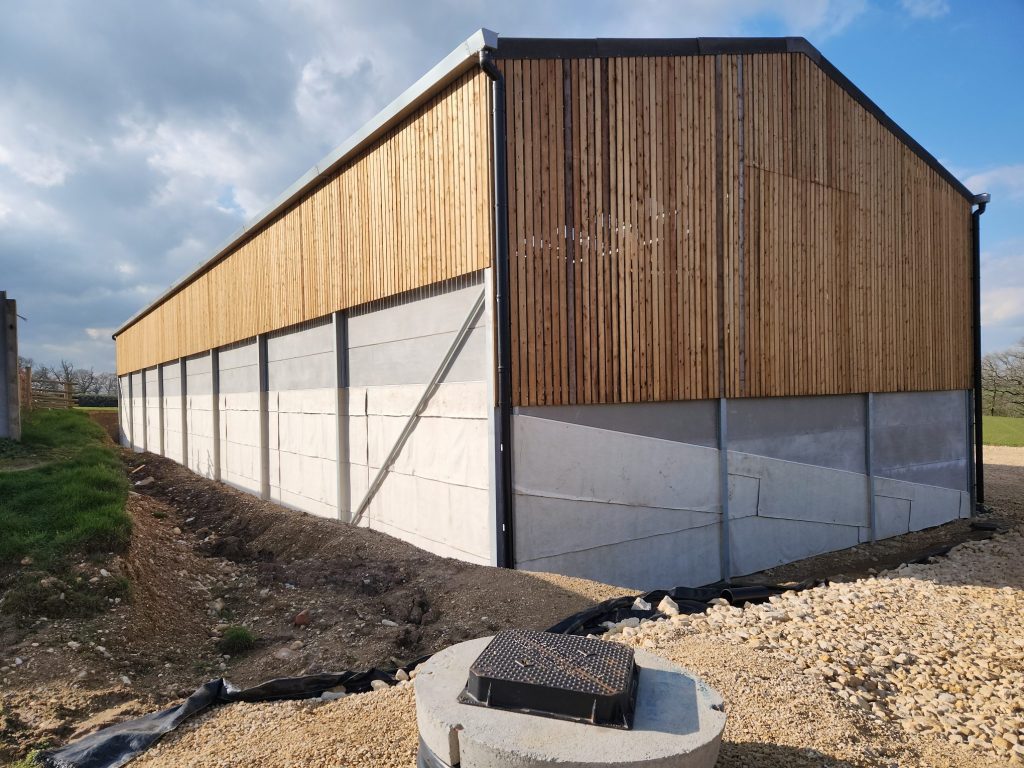
Internal cementitious waterproofing
The same slurries as external waterproofing, but unlike bentonite and bitumen, the slurry creates a mechanical bond with the substrate. This allows it to be applied “negative side” and will actually resist water ingress with the bond it creates to the substrate.
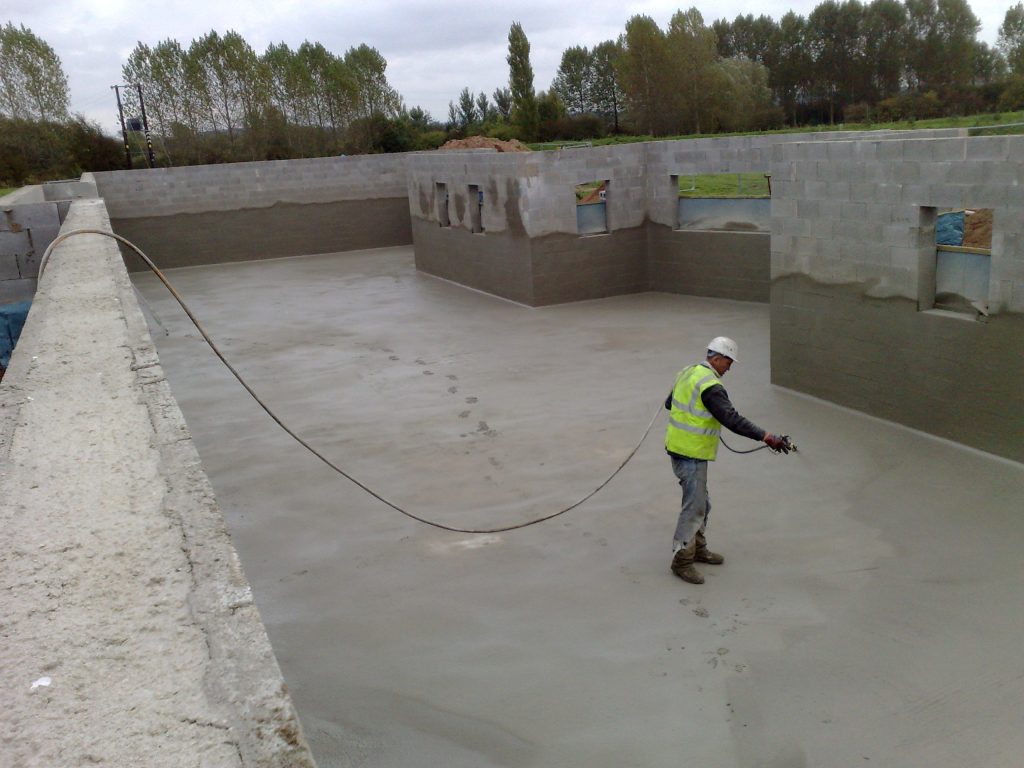
External bitumen coating
The external face of the basement walls are sprayed with a permanently homogenous bitumen with fibre-glass reinforcing between layers.
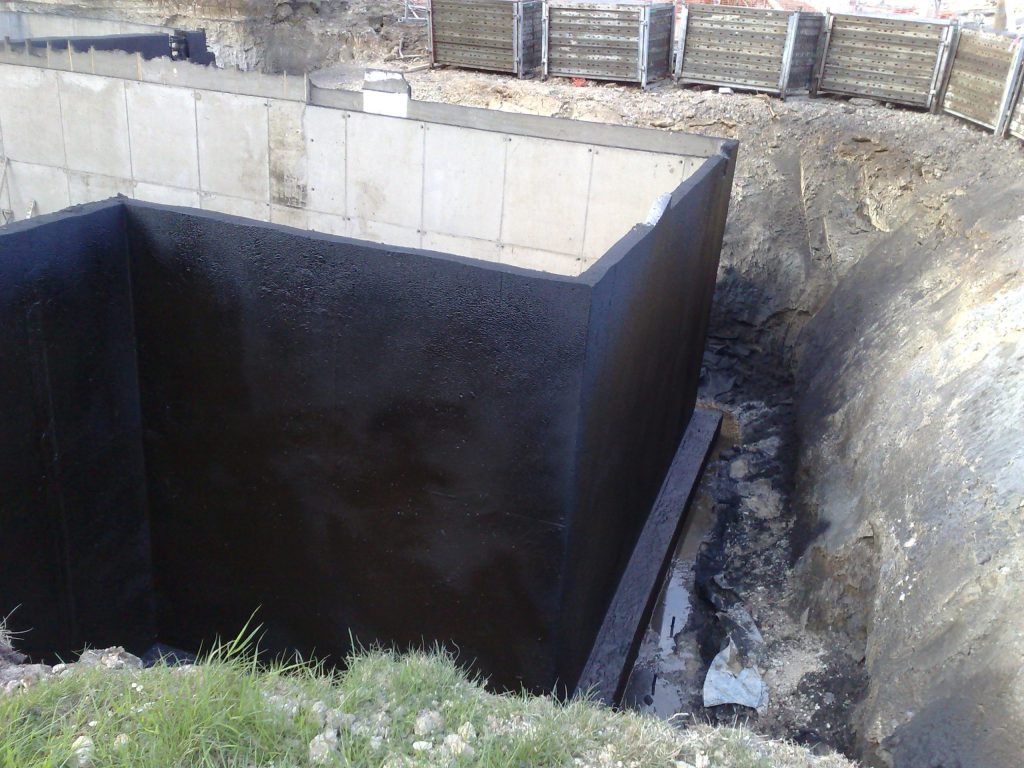
External cementitious waterproofing
This is a cement based, hydrophilic crystallising slurry, applied by brush or sprayed. As the slurry dries it bonds with the concrete face of the external walls and begins to crystallise into it upon contact with water.
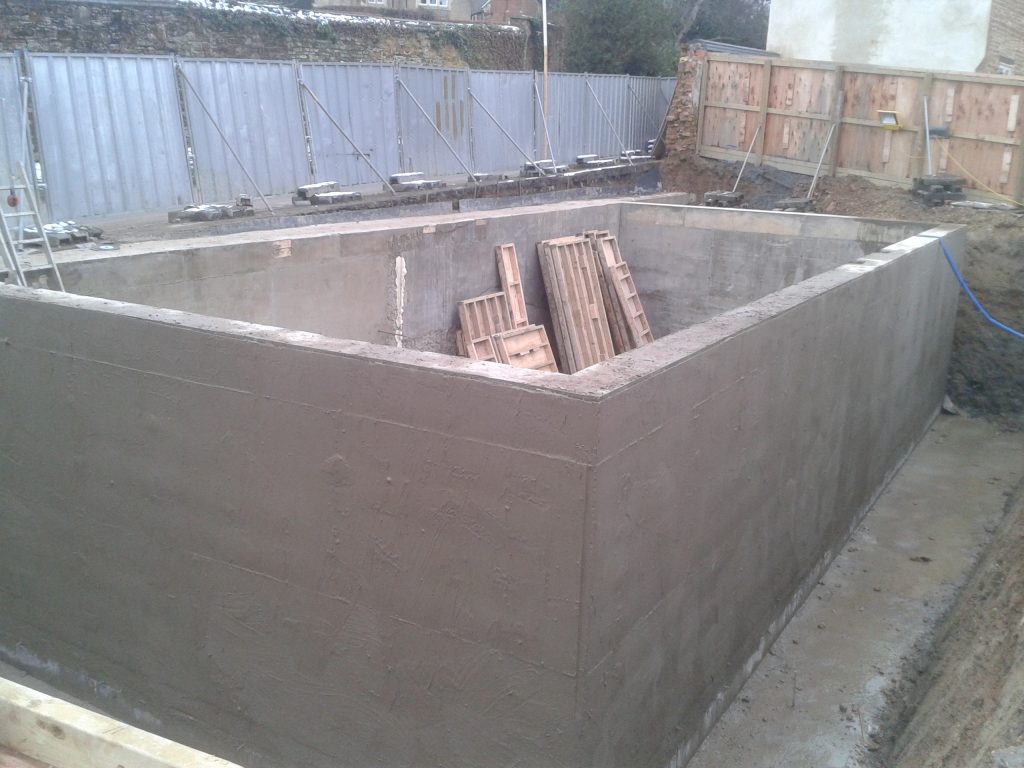
Type A combination waterproofing
In some very low risk situations, a combination of two type A waterproofing systems can provide the coverage needed. This relies on good soil / site drainage and very low risk circumstances to be an acceptable system.
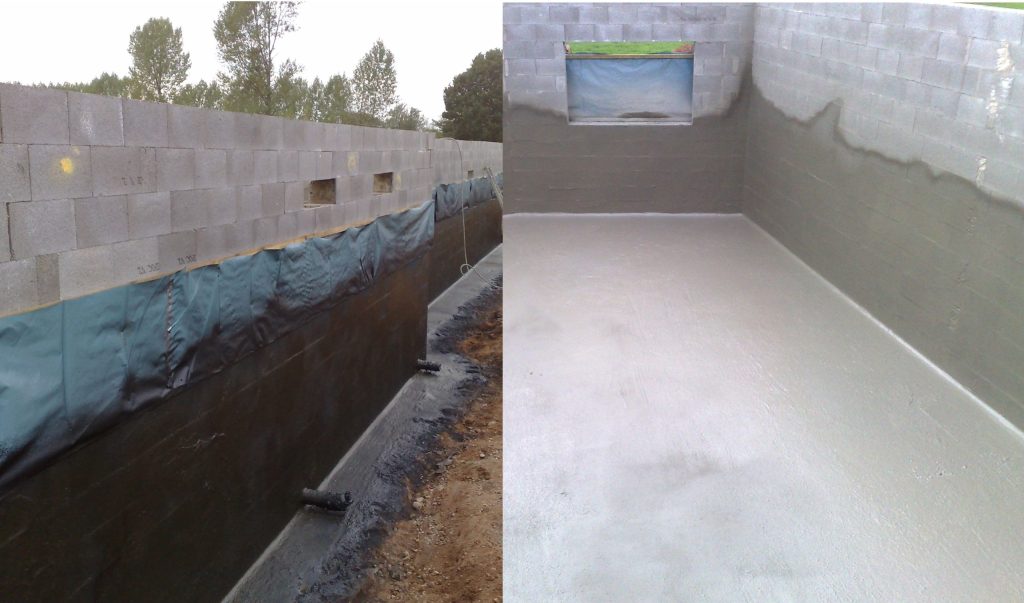
Type B – Integral protection
A type B system, like a type A, seeks to stop water from entering the basement with a physical barrier. This barrier, however, is provided by the structure itself. The basements retaining walls are designed by a suitable structural engineer along with Beautiful Basements to ensure that this is the case. It can be achieved by two methods:
- Wall reinforcing designed to BS8007:1987 where the crack width is limited to 0.2mm and becomes self-healing
- Design the concrete to have a waterproofing additive within in from the batching plant. This prevents shrinkage and cracking, stopping water from penetrating the building.
A type B system is also only appropriate for new build basements. Careful consideration must be given to placement of concrete and the ability to vibrate and move it around to achieve 100% coverage. For this reason, sandwich build systems such as insulated concrete formwork (ICF) and permanent block formwork should not be used with this system.
Waterproofing additive within the concrete
A waterproofing additive is combined during the production of the concrete at the batching plant. That concrete is then poured between the wall formwork and vibrated until 100% coverage of the space and steel is achieved.
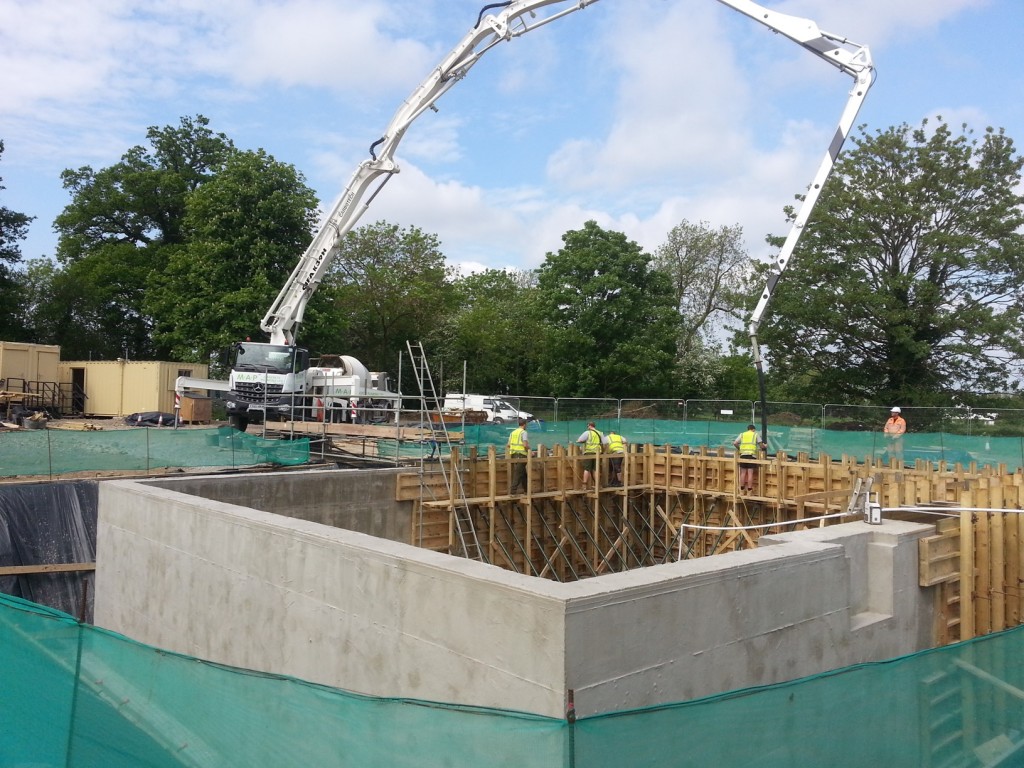
Waterproofing provided by steel & concrete design
Crack restriction by design of the concrete is one of the type b systems we install. The amount, type and placement of reinforcement steel within the concrete allows greatly reduced cracking and tracks for water, and is waterproof.
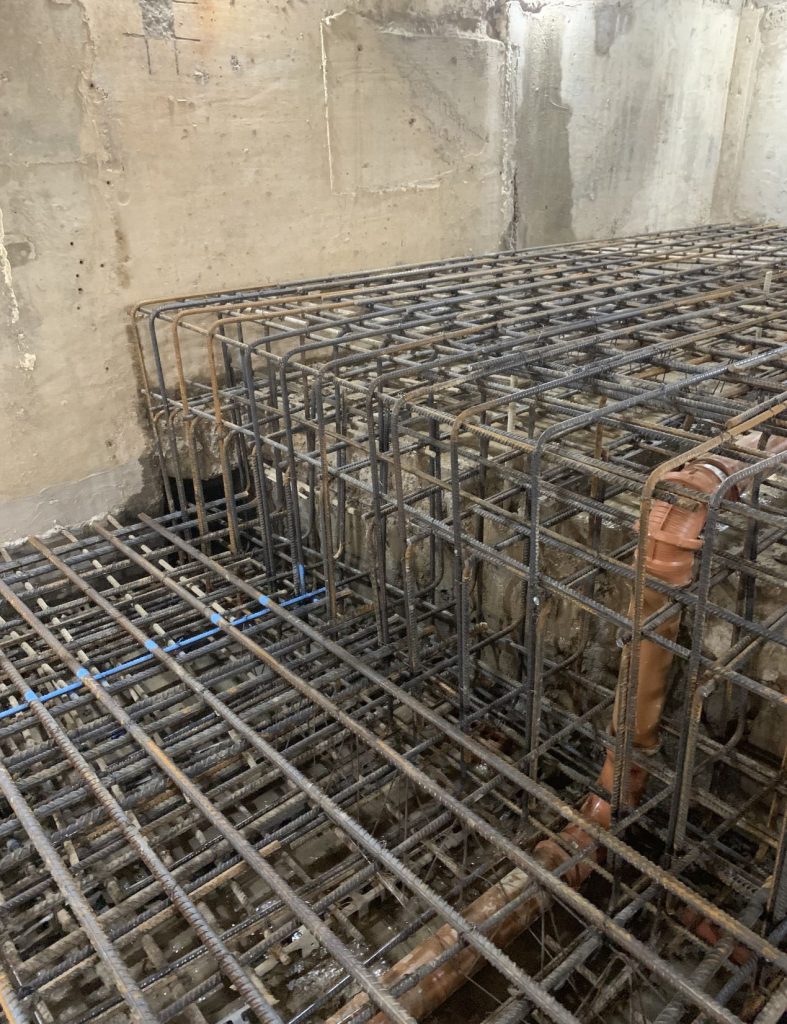
Type C – Drained cavity protection
A type C system is the most reliable system we install. Technically however, it is more of a water management system than a true waterproofing system.
The principal is to accept that some water will find its way through the structure of the basement. What you then do with this water becomes the waterproofing system. A cavity is created between the external walls, floor and internal finishing to allow water to be directed to a discharge point. Water can be removed with either a sump and pumping station or by gravity.
A cavity drain can be created one of the below ways
- Cavity drainage membrane
- Cavity formed by blockwork / brickwork
Formed cavity protection
This is a system we install only in relatively low risk environments. A cavity is formed between the retaining walls and the internal building finishes, the floor is lined with a cavity drainage membrane and linked to a damp proof course in the blockwork wall.
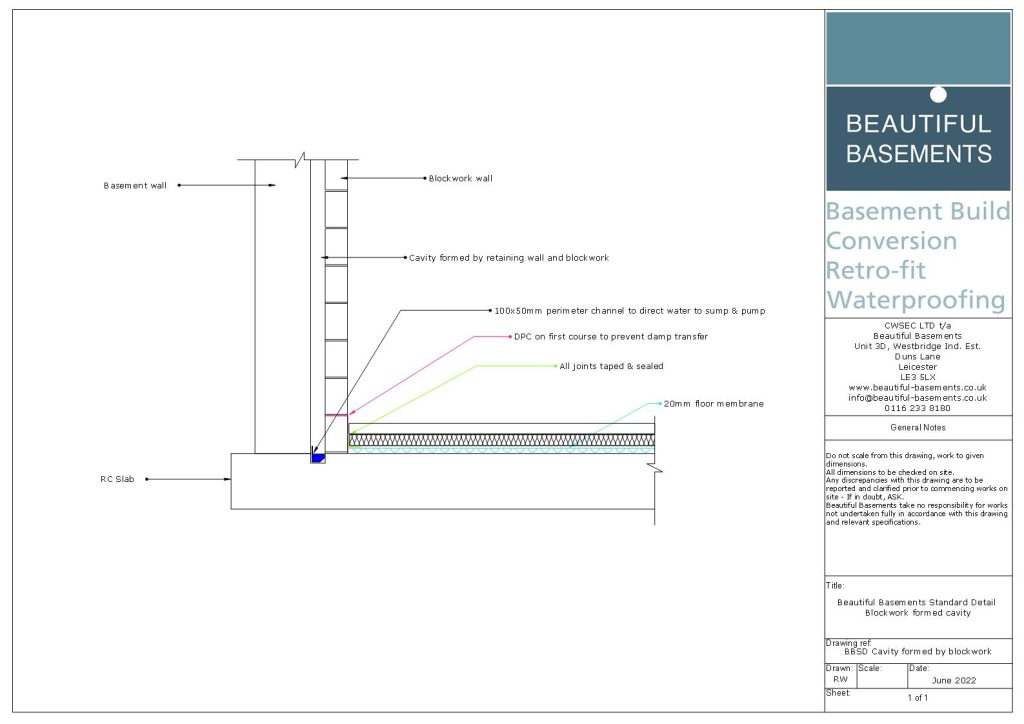
Cavity drainage membrane
The walls, floor and ceiling (if applicable) are lined with a tough plastic membrane with an “egg box” like construction that creates a cavity between it and the substrate. Any water that does come through the substate is then channelled to a sump & pump or away via gravity. The basement can then be finished “dry side” as any normal project is.
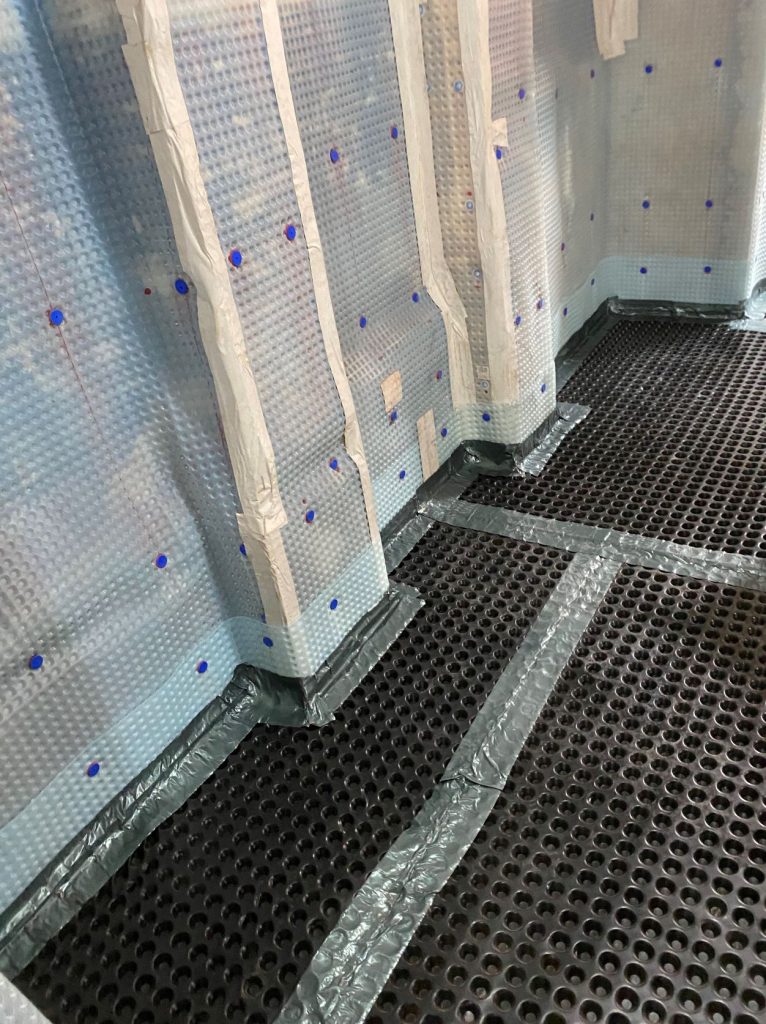
Combined systems
If you are looking to build a new house with a partly or fully underground section then you may require a third party warranty scheme. If this is the case, then you’ll need two of the above types of waterproofing system. The types that are included will depend on the risk profile and build type, but the common combinations are:
- Type A & B (internal or external type A)
- Type A & C (internal or external type A)
- Type B & C
Insurance backed guarantees
Midland tanking offers a standard 10 year guarantee on all waterproofing installations for free and can offer a 10 year insurance backed guarantee under written by Quality Assured National Warranties.
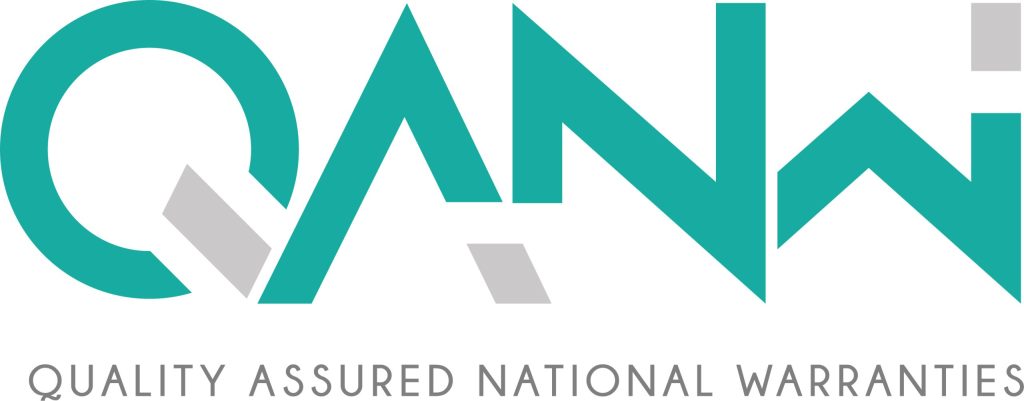
Midland Tanking Ltd are accredited designers and installers for the each type of waterproofing systems and the full range of the products offered by the waterproofing companies below. For more information on what products and applications they offer, click on the logos.